When it comes to service work, in general there is a problem, something has happened with equipment not working as it should and a solution needs to be found. Here are some case studies where Hundested Propeller has been involved in finding solutions to customers problems.
Hundested Service case study 1 Læsø Ferry
The Problem
It’s the 2nd December 2021 and the ferry for Læsø, M/F Margrete Læsø experienced a breakdown on their number two bow thruster. This breakdown although critical did not prevent the ferry from remaining in service.
The Hundested Propeller Solution
Clear communications and having a plan in place is critical. The breakdown of this number two thruster, did not put the ferry out of action and hastening to dock without a plan in place in place will only decrease uptime, and increase costs for the ferry company and ultimately a loss of income.
Following breakdown on the 2nd December the engineer of M/F Margrete Læsø contacted the Hundested Propeller Service Team to discuss their options. A plan was put in place that would see the ferry successfully dock in Orskov Yard in Frederikshavn on the 15th December and the thruster would be removed.
From here it would take just four days for the ferry to be back in service.
On 15th December a service engineer from Hundested Propeller was waiting to receive the thruster before driving to our factor in Hundested where the disassembly began, and a complete inspection was carried out. It was discovered that the input shaft had broken.
As the majority of Hundested Propeller spare parts are manufactured in house, we rarely have to wait for a shipment to come through. In this instance the input shaft was replaced, and the thruster swiftly reassembled. It was then put in the test bench, to check that it was working correctly and then ready to leave the factory.
On Sunday 19th December the thruster was transported back to Orskov Yard, where a Hundested Propeller Technician took care of the reinstallation and drove home to Hundested on the same day. The ferry went back into service on Monday 20th December, to pick up the busy holiday traffic.
Fast and efficient service is essential to many of our customers, therefore it’s an advantage that most of our parts, from drawing to manufacturing, are produced in house. We are highly flexible and able to adapt to a customer emergency when needed.
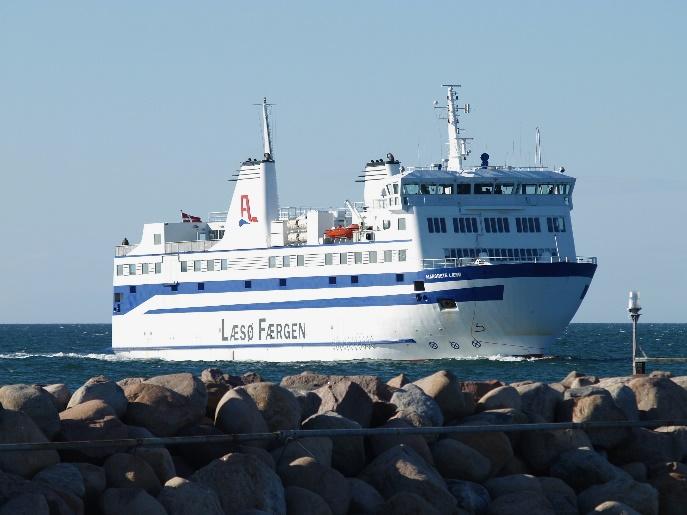